Band Dryer (Apron Type Dryer)
GENEX offers advanced and cost-effective band dryer machines tailored to the continuous drying needs of the food and chemical industries. As a leading band dryer manufacturer in India, we specialize in Continuous Belt and Tray Dryers engineered for industrial applications. Our single and multi-stage dryers are custom-built to client specifications, with widths ranging from 700 mm to 3250 mm and lengths from 10,000 mm to 45,000 mm. These dryers support multiple fuel options, including gas, steam, electricity, and thermic fluid. Available in both Stainless Steel and Mild Steel constructions, our machines reflect the reliability and performance expected from the best in band dryer manufacturing.
Capacity: Up to 2500 Kgs /Hr of Made Products
Depends upon input and required output moisture content of the product.
Major applications of our Band dryers are:-
Desiccated Coconut Powder, Coconut Chips, Coconut Threads, Coconut Flakes, Coconut Sugar, Virgin Coconut Oil DC Powder, Copra, Parings and various other products.
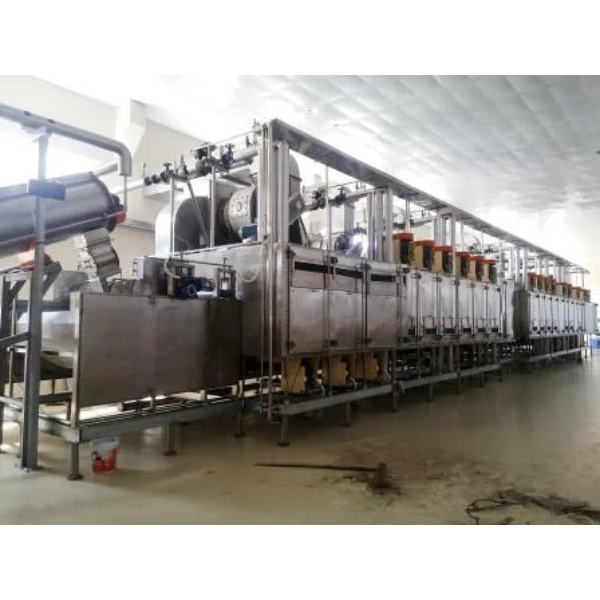
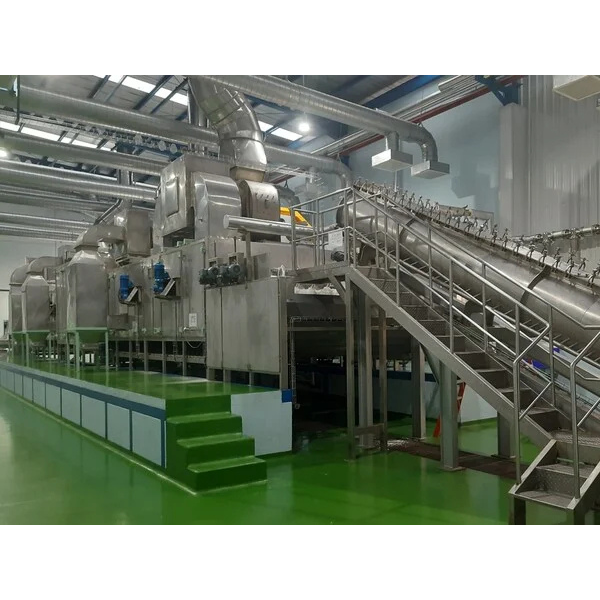
Salient Features
* Different Heating Zones
Separate Heating Coils in each zone allow the user to set different temperatures in each zone as per the requirement of the product. This allows for better control of the drying process and allows optimization of the output and the drying time. The Heating Coils in the dryer can be heated by means of Stearn, Gas, Electricity or Thermic Fluid.
* Variable drying time
Each Stage has a Variable Frequency Drive which allows the user to set different surface speeds for each stage and adjust the drying time of the product accordingly providing high flexibility and the desired amount of product moisture at the time of discharge. These dryers can be made in Single Stage, Double Stage or Triple Stage.
* Optimum Capacity
The output capacity of the dryer depends upon the chosen product and the input and output moisture and the residence time. With immense flexibility provided within the dryer, the equipment is designed to provide the optimum output for any given product.
* Controls and Instrumentation
A Control Panel to run the machine and to monitor the temperature in each zone is provided. Complete PLC and SCADA systems can also be incorporated minimizing human error. (Optional)
* Customer Service and Spare Parts
Our engineers Install and provide successful running trials of the equipment and train local engineers on how to clean and troubleshoot the equipment on a regular basis. Spare parts are kept in ready stock at all times to reduce downtime.